Laser Shaft Alignment Services
What is Shaft Alignment?
Shaft alignment is the positioning of the rotational centers of two or more shafts such that they are co-linear when the machines are under normal operating conditions. Proper shaft alignment is not dictated by the total indicator reading (TIR) of the coupling hubs or the shafts, but rather by the proper centers of rotation of the shaft supporting members (the machine bearings).
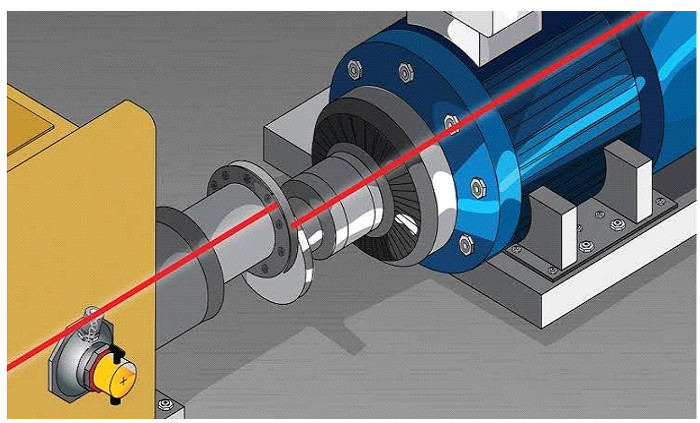
What is Shaft Alignment?
Shaft alignment is the positioning of the rotational centers of two or more shafts such that they are co-linear when the machines are under normal operating conditions. Proper shaft alignment is not dictated by the total indicator reading (TIR) of the coupling hubs or the shafts, but rather by the proper centers of rotation of the shaft supporting members (the machine bearings).
Types of Misalignment?
- Parallel or Offset Misalignment
- Angular Misalignment.
- Combined Misalignment
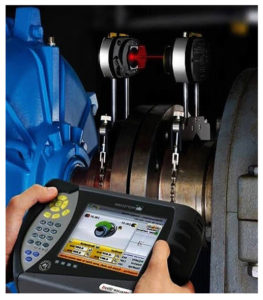
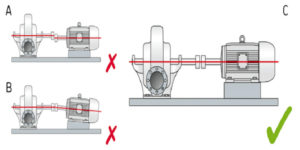
1. Reduced Energy Consumption
Significant power savings can be made through accurate alignment. Precise alignment eliminates reaction forces and reduces energy consumption by up to 10%.
2. Reduced Incidence of Repairs
Mechanical seal repairs decline by up to 65% when precision alignment is carried out on a regular basis.
The rate of repairs declines by up to 30% when precision laser alignment becomes an integral part of the pump repair schedule. Maintenance costs are also reduced through lower parts expense and inventory levels.
3. Longer Machine Life
Relation between offset and bearing life cycle: The smaller the offset misalignment, the greater the expected bearing life cycle.
4. Low machine vibration
Protects the assets and increases product quality as the vibrations are reduced to very low levels
5. MTBF
Extends the machine availability as the mean time between failure increases
6. Manpower cost reduction
Laser shaft alignment Increase in time savings and decrease in consumption of manpower for carrying out alignment.
How Bearing Life Is Affected By Misalignment
Formula notes: This formulation is credited to the work done by Lundberg and Palmgren in the 1940s and 1950s through empirical research for benchmarking probable fatigue life between bearing sizes and designs.
For ball bearings: L10 = (C/P)3 x 106; For roller bearings: L10 = (C/P)10/3 x 106
L10 represents the rating fatigue life with a reliability of 90 percent
C is the basic dynamic load rating—the load which will give a life of 1 million revolutions which can be found in bearing catalogues
P is the dynamic equivalent load applied to the bearing.