
Mechanical Integrity
Fitness for Services (FFS)
- Aging equipment can cause unexpected failures. Using Fitness for Service extends life of equipment, while avoiding expensive and unnecessary repairs.
- FFS is applicable to many components for several type of damage mechanisms. FFS assessments are conducted following the standard API 579/ASME FFS-1; recognized and referenced by other API Codes such as 510, 570, and 653.
- Should you repair or replace your equipment? Can it remain in operation? A Fitness-for-Service approach allows you to make informed decisions about the ability of the equipment to continue operating despite having flaws or damage.
- For pressurized components in power plants, chemical plants, or petrochemical plants the National Board Inspection Code is often the governing standard. This standard provides repair guidelines and allows for Fitness-for-Service approaches using ASME FFS-1/API 579.
- The initial FFS Level 1 evaluation is intended for use at the plant inspection level. An increasing level of complexity is required for the analysis of defects or conditions that do not pass the previous level.
- At the Level 2 evaluation, standard design calculations are made to take credit for any extra fabricated thickness, which can in turn be used as additional corrosion allowance.
- A Level 3 analysis is intended to be used by an engineering specialist in the appropriate field. At this level complex calculations are often employed, including finite element analysis and fracture mechanics
Benefits of FFS Assessments
There are numerous benefits to adding FFS assessments to an asset integrity management program. Conducting FFS assessments supports reliability of process facilities and reduces challenges related to expenditure and assessment completion time. Planning for an integrity assessment can save time collecting the data required to complete the assessment. Including FFS approaches as part of maintenance programs can save costs during facilities outages. Ensuring that these capabilities exist can reduce duration of shutdowns and potentially avoid unplanned shutdowns. MISTRAS has a proven track record in conducting comprehensive FFS assessments that have benefited industry operators by supporting:
- Operational and maintenance reduced costs
- Maintain mechanical integrity of assets
- Extension of assets service life and reduction of capital expenditure
- Compliance of regulation for a safe operation
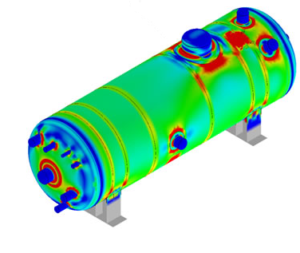
Structural Analysis Services
- Singlepeak Technologies expert engineers are proficient in analyzing the impact of external focus on static structures, such as construction components, machine components, and more.
- Our structural and stress analysis specialists help simulate the movement of non-stationary objects in vibration analyses, lifting analyses, and other services. With our technology and experience in structural stress analysis, we quantify and further rectify failures in the structure of components that do not meet the proposed design plan, which could result from improper use of materials or even flaws in the manufacturing process.
- Singlepeak Technologies offers you calculations and measurements of the statics of your components, complex assemblies and systems with and without FEM:
Structural analysis in mechanical engineering
- Statics describes the forces acting on resting bodies and their effects. Static analyses are used to determine the prerequisites for the state in which all static forces are in equilibrium with one another. After all, a machine or a steel structure should be and remain a stationary system. A supporting structure whose individual parts move in different directions collapses. To prevent this collapse in all load situations (wind, earthquake, collisions, weight) is the task of a static analysis in mechanical engineering.
- Various calculation methods are used in static analyses to determine the acting forces. A supporting structure must be designed differently from a piping system through which liquids of different temperatures flow. The strength calculation for a bracket made of a single metal alloy does not require the same approaches as the design of a structure made of different composite materials in lightweight construction. Our calculation engineers have specialized in statics in mechanical engineering and master the different approaches.
Structural calculation and design
- Singlepeak Technologies check the statics to see whether your construction can withstand all impacts such as additional loads, wind, snow, ice and earthquakes in addition to its own weight.
- A load-bearing structure is an overall system of load-bearing elements. A distinction is made between different types of load-bearing structures whose structure differs in terms of statics and shape.
- Beam structure: A beam structure is a structure whose load-bearing elements are composed of beams. These bars are connected to each other at their joints, the so-called nodes.
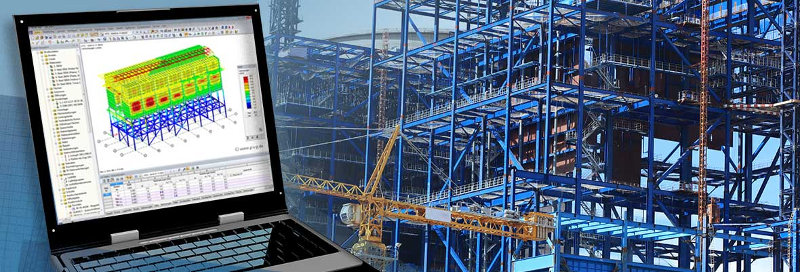
Structural Stability Certification
Structural Stability Certification by Government Approved Competent Person.
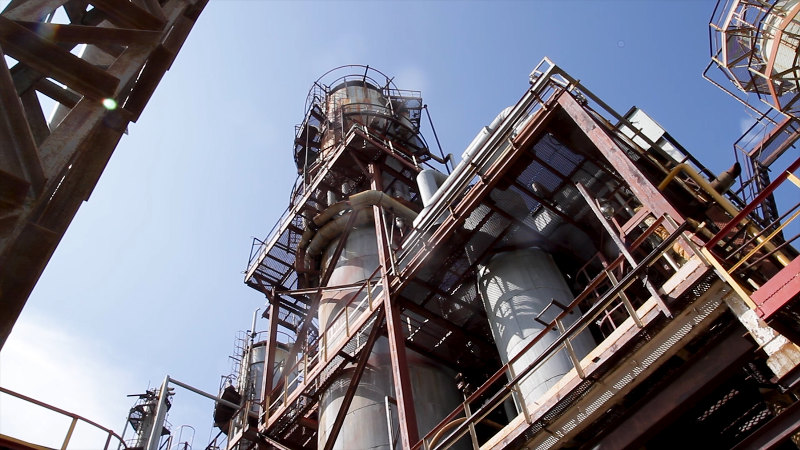
Certification Form-9, Form-10 and Form-11
- Form 9: Certification of Pressure Vessel
- Form 10: Certification of Hoists & Lifts
- Form 11: Certification of Lifting Machines, Ropes & Lifting Tackles
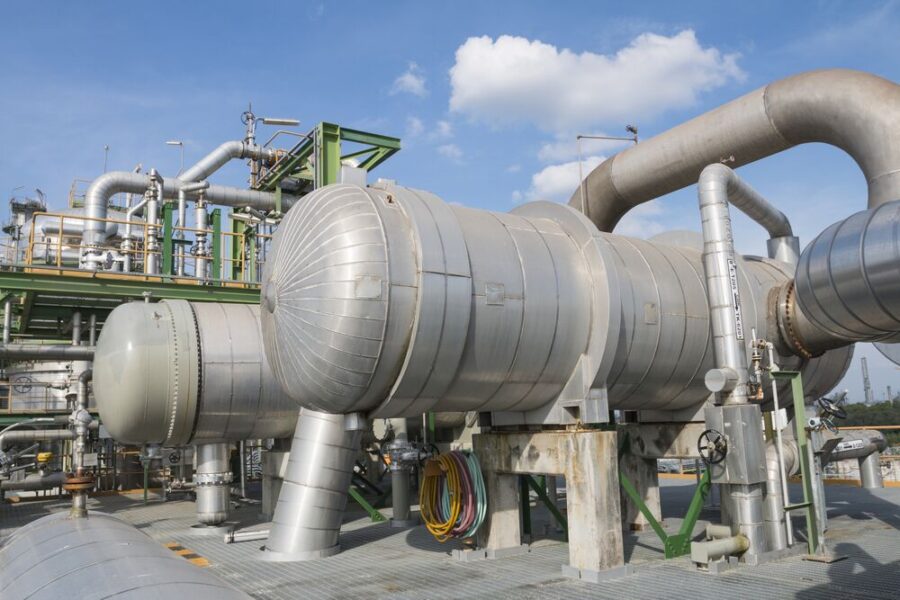