Thru Coat & High Temperature Thickness Measurement (EMAT Technology)
- Electro Magnetic Acoustic Transducer(EMAT) technology to enhance current UT inspections without requiring physical contact, measuring through a gap and does not need to be perfectly aligned.
- EMAT technology for thickness measurements. This method allows significant advantages over standard piezoelectric thickness gauges for the inspection process:
- No paint removal required (non-contact up to 4 mm)
- High temperature applications (- 20° C to +700 ° C)
- No surface preparation
- Use in corroded areas
- No couplant required
- Measures through unbonded paint
- Sensor not required to be perpendicular to test material
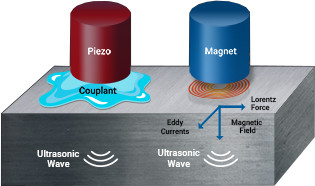
Eddy Current Testing
Eddy Current Testing (ECT)
Eddy current testing is a noncontact method used to inspect non ferromagnetic tubing.
- Application: Condensers, Feed Water Heaters Coolers, Evaporators, Chillers
Remote Field Testing (RFT)
Remote field testing (RFT) is being used to successfully inspect ferromagnetic tubing such as carbon steel or ferritic stainless steel.
- Application:
- Boiler Gen Bank tubes,Feed Water Heaters
- Carbon Steel Heat Exchangers
Other Testing
Internal Rotary Inspection System(IRIS)
Magnetic Flux Leakage (MFL)
Near Field Testing (NFT)
Internal Rotary Inspection System(IRIS)
Magnetic Flux Leakage (MFL)
Near Field Testing (NFT)
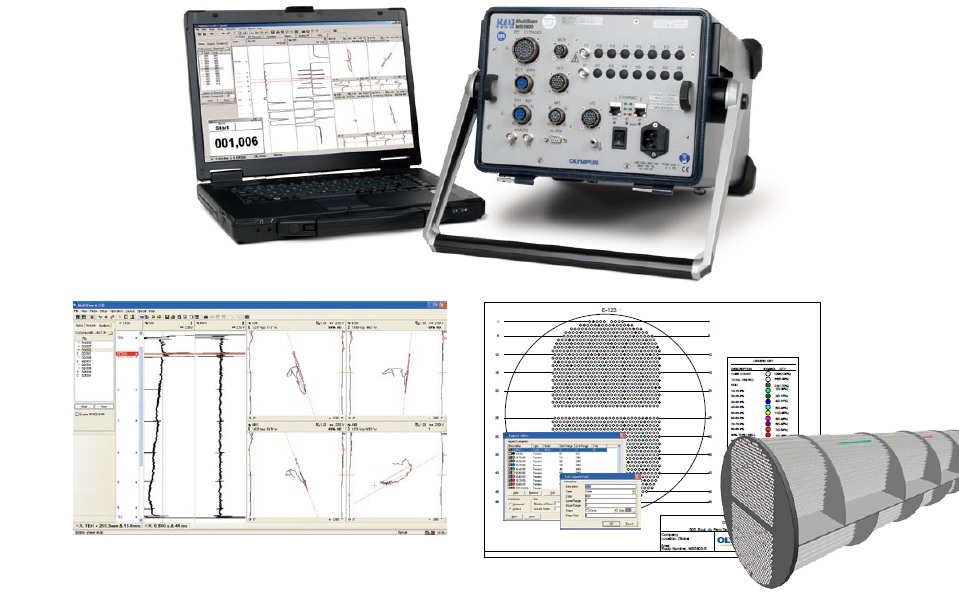
Borescopy Inspection
- Remote Visual Inspection or Remote Digital Video Inspection, also known as RVI or RDVI is a form of visual inspection which uses visual aids including video technology to allow an inspector to look at objects and materials from a distance because the objects are inaccessible or are in dangerous environments.
- RVI/RDVI is commonly used as a predictive maintenance or regularly scheduled maintenance tool to assess the “health” and operability of fixed and portable assets. RVI/RDVI enables greater inspection coverage, inspection repeatability and data comparison. The “remote” portion of RVI/RDVI refers to the characterization of the operator not entering the inspection area due to physical size constraints or potential safety issues related to the inspection environment.
Advantages of Visual Inspection/Videoscopy/Boroscopy
- Less mechanical disassembly to access subject areas.
- Reduced shut down times and faster reinstatement of equipment.
- Fewer safety constraints over manual inspection methods.
- Reduced NDT costs over other forms of testing.
- Better assessment of condition and timing prior to critical maintenance.
- Faster identification, location and isolation of faults.
- Faster, accurate monitoring of equipment condition during life cycles.
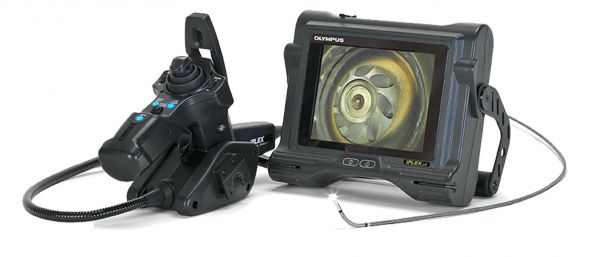